
|High Vacuum Equipment-Glossary of Terms
Please note that the following are general features and subject to change depending on processing conditions. For details, please contact sealing component manufacturerers.
FKM (Fluororubber)
With low outgassing, low permanent-setting and low gas permeation rates, this is the most popular seal material for high vacuums. Standard material used by SMC’s high vacuum angle valve is Mitsubishi Cable Industries, Ltd. (Compound No. 1349-80). It is advisable to choose a model depending on its application, because an improved material compound (3310-75) which reduces the weight reduction ratio with O2 plasma is also available.
Kalrez®
∗ Kalrez® is a registered trademark of DuPont Elastomers. This material, perfluoroelastomer (FFKM), has excellent heat and chemical resistance, but its permanent-setting is large, and special caution is required. Variations are available with improved plasma (O2, CF4) and particulate resistance; therefore it is advisable to select types based upon the application. Compound No. 4079: Standard Kalrez®, excellent in gas and heat resistance.
Chemraz®
∗ Chemraz® is a registered trademark of Greene, Tweed & Co. This material, perfluoroelastomer (FFKM), has excellent chemical and plasma resistance and has slightly higher heat resistance than FKM. Several variations of Chemraz® are available and it is advisable to choose based upon the particular plasma being used and other conditions, etc. Compound No. SS592: Excellent physical properties and especially effective for moving parts. Compound No. SS630: Applicable to both fixed and moving parts and compatible with a wide variety of applications. Compound No. SSE38: The cleanest material among Chemraz®, developed for high-density plasma instruments.
Barrel Perfluoro®
∗ Barrel Perfluoro® is a registered trademark of Matsumura Oil Co.,Ltd. Compound No. 70W: Perfluoroelastomer (FFKM) which does not contain a metal filler. Resistant against NF3, NH3. Low particle generation under dry process conditions.
ULTIC ARMOR®
∗ ULTIC ARMOR® is a registered trademark of Nippon Valqua Industries, Ltd. Fluoro-based rubber which does not contain a metal filler. Seal material which is plasma-resistant and has low gas emittance and heat resistance.
Silicone (Silicone rubber, VMQ)
This material is relatively inexpensive, has good plasma resistance, but its gas permeation rate is high. Optional seal material used by SMC’s high vacuum angle valve is Mitsubishi Cable Industries, Ltd. (Compound No. 1232-70, White) It has a low weight-reduction ratio and low particle generation within O2 plasma and NH3 gas environments.
EPDM (Ethylenepropylene rubber)
Relatively lower priced and excellent in weatherability, chemical and heat resistance, but with no resistance at all to general mineral oil. Optional seal material used by SMC’s high vacuum angle valve is Mitsubishi Cable Industries, Ltd. (Compound No. 2101-80) Resistant to NH3 gas, etc.
Bellows offer cleaner sealing with reduced particle generation and less outgassing. The two major bellow types are: Formedbellows and Welded-bellows. Formed-bellows produce less dusts and offer higher dust resistance. Welded-bellows allow longer strokes, but generate more dust particles and offer less dust resistance. Please note, the endurance depends on length and speed of the strokes.
O-ring, etc.
Due to entrainment of gases and generation of particulates, vacuum performance is somewhat inferior to the bellows type. However, high speed operation is possible and durability is comparatively high. In general, fluorinated grease is affixed to the shaft seal portion.
The time from the application of voltage to the actuation solenoid valve (XL□) until 90% of the valve stroke has been completed is the valve opening response time. Valve opening operation time indicates the time from the start of the stroke until 90% of movement has been completed. Both of these become faster as the operating pressure is increased.
Valve closing
The time from the cut off of power to the actuation solenoid valve (XL□) until 90% of the valve return stroke has been completed is the valve closing response time. Valve closing operation time indicates the time from valve opening until 90% of return movement has been completed. Both of these become slower as the operating pressure is increased.
In the case of a øA (cm2) hole in an ultra-thin plate, conductance “C” results from “V”, the average velocity of the gas; “R”, the gas constant; “M”, the molecular weight; and “T”, the absolute temperature. From the formula C=11.6A (L/sec) at an air tempearture of 20°C.

Cylinder conductance
With length “L” (cm) and diameter “D” (cm) where L>>D, from the formula C=(2πRT/M)0.5D3/6L, the conductance C=12.1 D3/L (L/sec) at an air temperature of 20°C.
Short pipe conductance
From the Clausing’s factor “K” and hole conductance “C” in Graph 1. (Clausing’s factor drawing), the short pipe conductance CK is easily found as CK=KC.

Conductances combined
When each of the separate conductances are given as C1, C2 and Cn, the composite conductance ΣC is expressed as: ΣC=1/(1/C1+1/C2+···+1/Cn) when in series, and ΣC=C1+C2+···+Cn, when in parallel.
This is a phenomenon where gases adhered or adsorbed to the metallic surface or its inside parts are released from the surface and drawn into the vacuum according to the pressure decrease. The smoothness of the surface and closeness of the oxidized layer can effect (increase/decrease) this.
Ultimate pressure P (Pa) is P=Q/S, where the sum of Weight flow rates for outgassing (Qg) and leakage Q(L) is Q(Pa·m3/s), and the exhaust speed is S(m3/s). The ultimate pressure is measured with Qg, Q(L)S shown as above, and the ultimate pressure of the pump itself. In the case of very low pressure, the exhaust characteristics of the actual pump can be the limiting factor. In particular, a deterioration of exhaust characteristics due to an unclean pump and invasion of the atmospheric moisture can be the major factor.
The time (Δt) required to exhaust a chamber at low vacuum with volume V (L), from pressure P1 to P2, using a pump with pumping speed S (L/sec) is Δt=2.3(V/S)log(P1/P2). In high vacuum, this is subject to the ultimate pressure limit imposed by outgassing and leakage as characterized above.
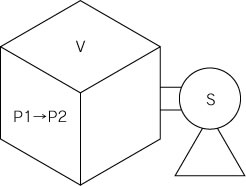
Gases such as oxygen and nitrogen, which have a small adsorption activation energy (E) and a short adsorption residence time (τ), are evacuated quickly. However, in the case of water, which has a high activation energy, evacuation does not progress quickly unless the temperature (T: absolute temperature) is raised to shorten residence time. This time is characterized as τ=τ0 exp(E/RT) where R is the ideal gas constant and τ0=(approx.) 10-13 sec. Residence time of water at 20°C is 5.5 x 10-6 sec, whereas at 150°C, it is 2.8 x 10-8 sec, or about 200 times shorter. The objective of baking is to exhaust water with long adsorption residence time more quickly.